Benefits for EVs
Increasing EVs’ safety and efficiency with composites
As the world of mobility travels towards a greener future, the materials used in vehicle component manufacturing are evolving. Discover why composites play a pivotal role in the electric transition with their non-conductive, fire-proof, and anti-magnetic properties.
Better for the batteries
One of the critical challenges in electric mobility is ensuring battery safety, reliability, and longevity. Firstly, composites can be engineered to have low thermal conductivity, making them ideal for managing the generated heat. For example, polymer matrix composites reinforced with materials like glass or aramid fibers provide an effective thermal barrier, reducing the risk of thermal runaway. In turn, composites deliver excellent insulation, effectively helping to maintain battery voltage in the coldest conditions. Secondly, composites, such as fiber-reinforced polymers, are inherently non-conductive, making them excellent electrical insulators capable of preventing short circuits.
Ensuring electrical functionality
Sensitive electronic components, such as digital panels, driver-assistance systems and autonomous driving technologies, must be protected from external electromagnetic fields. Composite materials provide efficient EMI shielding, enabling integrations of sensors and other electronic devices without the risk of interference. While metals such as copper, aluminum, and nickel are commonly used for EMI shielding, composite materials deliver lighter, more flexible solutions.
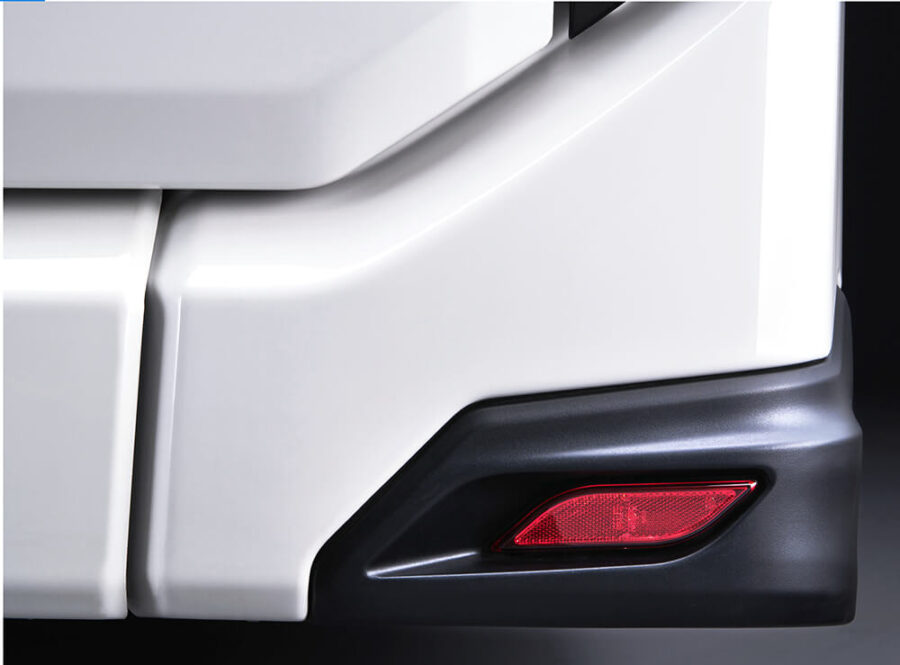
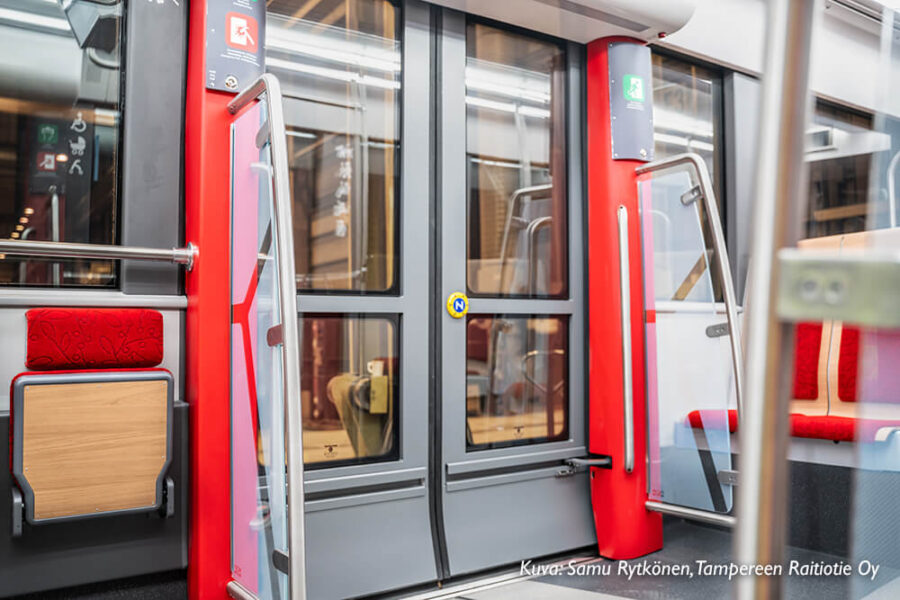
Added comfort
Maintaining an optimal temperature is crucial for vehicles’ performance and comfort, especially in cold climates where low temperatures can reduce battery efficiency and driving range. Due to low thermal conductivity, manufacturers can integrate heating elements directly into composite structures, creating more efficient and safer thermal management systems and allowing precise temperature control.
Fire-proof security
Fires in electric vehicles, while rare, can be particularly challenging to manage due to the nature of lithium-ion batteries, commonly used in EVs. These batteries can burn at extremely high temperatures, exceeding 1,000 degrees Celsius (1,832 degrees Fahrenheit), and may reignite even after being initially extinguished. Flammable electrolytes within the battery cells add to the fire risk. Using fire-resistant composite materials efficiently prevents fires from spreading, enhancing overall safety and allowing passengers more time to evacuate in an emergency. While the level of fire resistance varies depending on the material and application, modern fire-proof composites are engineered to provide robust protection, often enduring fire exposure for up to several hours.
Enhanced performance, durability and safety
Composites offer superior durability and impact resistance also for electricity. They can be designed to absorb and dissipate energy more effectively than metals, providing better protection in a collision. Additionally, composites are resistant to corrosion, extending the vehicle’s lifespan and reducing maintenance costs.
Lico at your service: the earlier, the better
With Lico, the cooperation with designers is straightforward. As a trusted Finnish company with 30 years of experience and ISO quality and environmental standards, Lico meets its clients’ expectations. After the successful design phase, Lico produces a prototype to which slight changes can still be made. The optimal amounts for serial production vary from 100–2000 items. The company uses local subcontractors and proven European logistic operators in its supply chain.
The best benefits are delivered when a composite solution provider is included in the project from the design phase. The client owns the IPR for product shape and measures, and Lico ensures the design is optimized for usability, sustainability, and manufacturing.
Arto Pitkämö
CEO, Sales and Marketing
+358 400 917 282
arto.pitkamo@lico.fi